The UNiBLOCK System
UNiBLOCK is more than just an insulated concrete formwork block, our solution includes a full range of accessories and services to support your project

Insulated Concrete Forms
Central to the UNiBLOCK ICF system is the block which is constructed with a combination of expanded polystyrene (EPS) and steel wire mesh reinforcement. This results in an incredibly robust wall, which will perform much better than standard ICF with plastic ties. The block is the largest on the market, covering an area of 16 sq ft (1.44m2) per wall. Its large surface and straightforward design allow for efficient and cost-effective installation on the construction site
UNiBLOCK offers the Xpress Wall pre-cut system, which is a unique proposition in the ICF market in the UK. We take your plans and design the ICF wall layout using software specifically programmed to create a list of cuts to make to form each opening and corner. We then optimise this for production and cut and number each block according to the agreed plans, making on site installation faster. The Xpress Wall system is recognised as a Category 2 MMC (Modern Method of Construction) and is ideal for builders and developers who want to embrace offsite methods without the challenges of other modular systems
The superior U-Value of the UNiBLOCK Xpress Wall system (as low as 0.14 w/m²k) means that homes and commercial buildings constructed from UNiBLOCK are both thermally and sound efficient.
In addition, Xpress Wall by UNiBLOCK has highly impressive air tightness results of 0.73 ac/h (which is below the n50 Passivhaus definition Heated Building volume at 50pa) or 0.14 m3/(h,m2) under the surface area Q4pa calculation.
The Block Technical Specifications
-
Outer leaf of 75mm, 110mm or 150mm High performance graphite EPS
-
Inner leaf of 75mm High performance graphite EPS
-
An integrated steel strip in both the external and internal panels provides a fixing point for external cladding and internal installations.
-
Embedded wire mesh with a patented folding mechanism enables blocks to be flat-packed for delivery and increases overall strength.
​
​

Panel Size | Weight | U Value | Core Thickness Available |
---|---|---|---|
150mm | 18kg | 0.14 w/m2 | 155, 200, 250 & 300mm |
110mm | 16kg | 0.17 w/m2 | 155, 200, 250 & 300mm |
75mm | 15kg | 0.21 w/m2 | 155, 200, 250 & 300mm |
ICF System Accesories
​​
UNiBLOCK has a wide range of accessories to complement the ICF block including:
​
-
Cavity Closer and Frame Acceptor System - Made from 100% recycled materials, CAVALOK cavity closers are the market-leading cavity closer system. One of the simplest yet most effective ways of sealing cavities around wall openings, the CAVALOK Big Block system works seamlessly with the Xpress Wall block, creating a permanent shutter around each opening as well as the subframe to accept the windows and doors. Using the CAVALOK frames removes the need for creating temporary shuttering around openings, as well as eliminating potential thermal bridging issues.
-
Base Track - The base track ensures the wall is plumb during first row placement, base track sections are shot-fired into the slab or foundation and can also provide and extra fixing point at the base off the wall.
-
Wall Bracing System - ICF bracing systems are available to hire from UNIBLOCK as part of the system. We have a selection of Giraffe and Plumwall braces available, as well as corner formers. The braces are an essential part of the build process, as they keep the wall stable and plum during concrete placement.
-
Cladding Systems - Finishing system options for ICF are almost limitless. The most common being brick slip or thin-coat renders, however a wide range of other cladding options are available including timber and composite systems. At UNIBLOCK, we have partnerships with suppliers who specialise in these systems and can gladly help you find the right option for your project.

Project Support
As a provider of offsite building solutions, we understand that building with an MMC like the Xpress Wall system can be very different from traditional methods. Part of our product offering is to take away some of the on-site decision making and potential for error and to deliver key elements of the build from within our factory.
​
From initial concept, our team will work with your design team to optimise the Xpress Wall system, ensuring that the final product meets the relevant design and buildability criteria set down. Once finalised, the drawings are issued for final client approval, before being sent to our factory for production to commence.
​
At this stage we will commence training for those who have not built with our system before. This can consist of:
​
-
In-factory familiarisation at our Scunthorpe office
-
Site pre-start assessment
-
Day one setting-out.
-
Pre-concrete pour check.
-
First concrete pour guidance.
​
For professional builders, this training can be anywhere from 1-2 days depending on experience and skill levels.
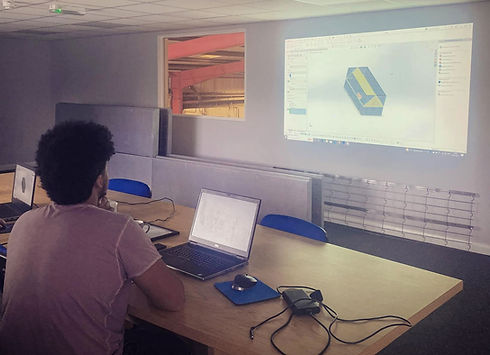